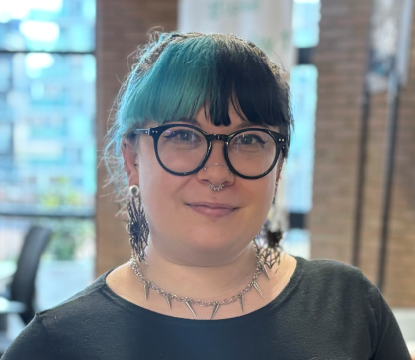
It’s been a challenging few years for the food and drink sector, which has navigated new customs requirements under the UK’s Border Target Operating Model (BTOM), with increased security measures introduced recently in response to a European outbreak of Foot and Mouth Disease.
This week, we spoke to Sophie Lavis, Flora Food Group’s European compliance and customs manager, who explained how the company has tackled these challenges, as well as preparing for US tariffs, which were announced last month.
Lavis also discussed how the Chartered Institute of Export & International Trade’s courses have supported her career development and grown her team’s customs capabilities.
Export network
Flora Food Group supplies over 100+ countries worldwide, with a range of delicious products across four categories of butters & spreads, creams, culinary and cheeses..
Flora is setting up a factory in the US, having just “acquired an empty one and changing it to our specifications”. This has taken the sting out of the recent wave of reciprocal tariffs.
Reflecting on the factory refurbishment, Lavis says Flora Food Group still isn’t immune, and that timing is also everything. She says that, while refurbishment is under way “right now, most of our American products are in Europe – Germany specifically”.
Navigating border delays
The majority of the company’s spreads are plant-based or contain minimal dairy.
This means they’re classed as composite products, and are therefore not subject to checks under the UK’s BTOM or comparable regulations introduced by the EU on UK food and drink exports.
However, this doesn’t stop overzealous port health authorities from trying to stop goods, believing them to contain animal products. This was especially the case in the wake of the European Foot and Mouth Disease outbreak.
Flora works with them to explaining the specification of their products and finding solutions such as completing low-risk Customs Health Entry Documents (CHED). Lavis says:
“This time, they wouldn't back down until we completed a low-risk CHED and obviously you have to pay for them, plus we’re not set up for that because it’s not required.”
To overcome hold-ups with composite products, Lavis advises companies to have an open dialogue with the port health authorities relevant to them, saying that after speaking to a “wonderful couple of guys” who helpfully advised on which documents should be sent with products to prevent needless delays.
“We plan to start with the worst product [for hold-ups],” she says, “which keeps getting delayed, and then work through others”.
Lavis also flags that the language used to market plant-based products that mirrors meat goods can also exacerbate scrutiny at the border, making it something worth evaluating in the event of multiple delays.
Sustainability
It’s not just costs and customs driving the company’s efforts to enhance transport efficiency; Lavis says this also aligns with Flora Food Group’s sustainability goals.
In the case of goods moved by road freight, she says “we’re always asking ‘how can we consolidate, rather than doing three half loads – how can we turn that into 1 ½ loads”.
Often, it’s a case of only delaying or bringing forward a load by a single week.
She says the same logic is applied to the time taken for goods to clear customs, having compared the time taken for the team to find and approve Flora’s goods manually, with the use of a Goods Movement Reference (GMR), which she says is “pretty much automatic for us”.
She reiterates that the time gained isn’t just good for Flora’s reputation or its bottom line, but can make a meaningful difference to its carbon footprint.
“During that time waiting, a chill truck is still staying chill, it's burning through fuel via electricity or diesel, so we’re really quite mindful about it.”
Development
Lavis says she became a fully-fledged “customs nerd” during the Brexit transition, when she used government grants for customs education.
This was when she caught the training bug, embarking on several UK Customs Academy training courses, co-delivered by the Chartered Institute, with colleagues.
Having structured learning alongside the role helped to stretch her capabilities. She describes the process of moving from Level 2 – “I know that I do this in my day job” – through to Level 3 – “OK, this is getting wider, more difficult” – to completing her Level 4 qualification in December.
Advancing through the courses has supported her progression from analyst within Flora’s customs team to European compliance and customs manager.
She adds that it’s also a great way to keep engaged but create boundaries as someone who “can’t just turn off at the end of the workday”.
“I just can't stop and it's great fun.”
To learn more about our membership options, including professional, business and supplier, click here.